In the pursuit of environmental sustainability and health consciousness, many consumers are turning towards glass water bottles as a preferred choice. The benefits of glass water bottles are vast, and understanding the manufacturing process is crucial for those interested in sourcing or producing high-quality products. Glass water bottle factories are at the heart of this eco-friendly movement, offering a durable, reusable, and stylish option for consumers worldwide.
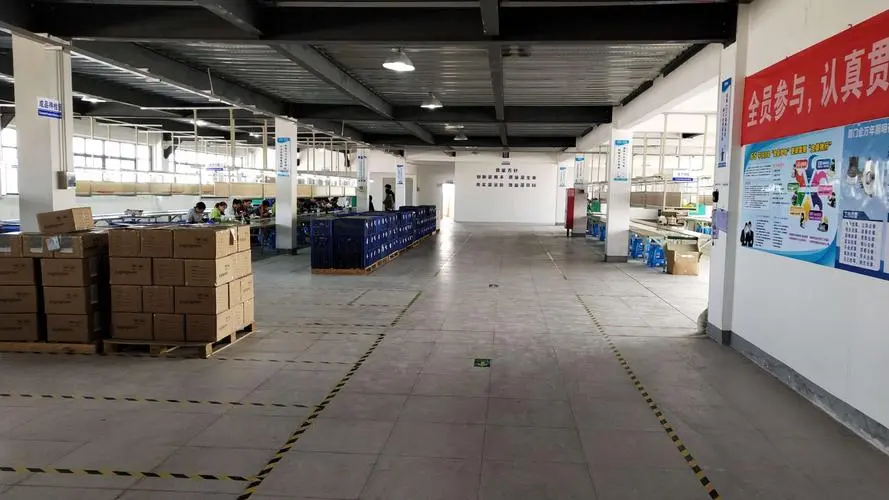
The journey of a glass water bottle begins with high-quality raw materials. The primary ingredient is silica sand, which is abundant and ensures the glass is both strong and clear. Other materials like soda ash and limestone are added to reduce the melting temperature and improve the chemical durability. The expertise involved in selecting and combining these materials cannot be overstated. Expert technicians must ensure the precise composition to provide the perfect balance of clarity, strength, and lightness.
Once the raw materials are carefully measured and mixed, they are melted in a furnace at temperatures exceeding 1700 degrees Celsius. This intense heat transforms the raw elements into molten glass, a process requiring state-of-the-art machinery and experienced operators. Factories employ cutting-edge technology to maintain the exact temperatures and conditions needed, ensuring that the molten glass achieves the desired quality and consistency.
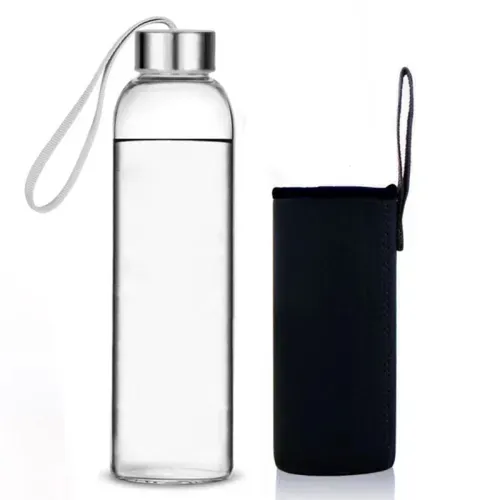
After reaching the optimal molten state, the glass is formed into bottles using a process called 'blowing.' This involves expert craftsmanship where molten glass is shaped using a combination of air pressure and molds. Skilled professionals ensure that each bottle is uniform in thickness and shape, which is critical for both aesthetic and practical reasons. Factories often implement rigorous quality control measures to detect and discard any defects, further demonstrating their commitment to delivering products that meet the highest standards.
glass water bottle factory
Moreover, the role of automation and human expertise blends seamlessly in modern glass water bottle factories. While machines handle repetitive and heavy tasks with precision, human craftsmen are tasked with overseeing the quality and customizing the designs as per client specifications. This synergy between man and machine enables the production of aesthetically pleasing and ergonomically designed bottles that appeal to a wide range of consumers.
Safety and sustainability are also paramount in these manufacturing units. State-of-the-art facilities prioritize creating a safe working environment for their staff by adhering to international safety standards. Additionally, modern glass factories implement recycling processes where cullet (recycled glass) is used to reduce energy consumption and carbon emissions. These efforts highlight the commitment of glass manufacturers to environmental stewardship, making their products appealing to eco-conscious consumers.
Finally, trustworthiness and authority in the glass water bottle industry are built over years of consistent quality and innovation. Leading factories often have certifications that vouch for their manufacturing excellence and adherence to environmental guidelines. Being transparent with clients about the sourcing of materials and production processes fosters trust and establishes a factory's reputation as a reliable and authoritative entity in the market.
In summary,
glass water bottle factories embody a perfect blend of tradition and innovation. Their commitment to excellence, sustainability, and safety with a keen focus on quality makes them a cornerstone in the push towards environmentally friendly consumer products. For anyone invested in the glass water bottle market, understanding the production process enhances appreciation for the craftsmanship and expertise involved, adding a layer of credibility and authority to their choice of product.